When it comes to rolling door curtain materials and finishes, there’s no shortage of options. So, how do you know which one is right for your project? It depends on several factors. The primary ones are application and the environment where the door will be used. Additional considerations, such as aesthetics and budget, also drive the decision. Let’s dive into rolling door material and finish options, benefits and drawbacks:
Steel
Steel is a popular material choice for rolling doors since it is durable, readily available and meets the requirements for many standard applications. Steel doors are typically galvanized, pre-painted or powder coated.
Galvanized Steel – with this process, the steel is zinc coated, giving it strong protection against rust and corrosion. Galvanizing is generally the lowest cost option, producing a finish that lasts a long time. The biggest drawback? It’s not the most attractive finish, but it certainly gets the job done.
- Good for industrial applications requiring durability with lower cost
- Base material of g60 quality to prevent pitting and rust
- Available in gauges 24-12 based on size and application
Pre-painted Steel – here, the steel has a baked enamel coating. It’s another popular, budget friendlier option. However, color choices are limited, usually to less than a handful. Often pre-painted doors are only offered in one color. (Reminds us of that famous Henry Ford quote, “Any customer can have a car painted any color… so long as it is black.”) Pre-painted doors are also more prone to scratching, as the enamel is not as thick and durable as powder coating.
- More attractive than galvanized steel
- Great for industrial / commercial applications, where an additional coat of protection is required, and looks are of concern
- Available in gauges 24-18 based on size and application
STAINLESS Steel – more demanding rolling door applications require stainless steel, available in grades 304 and 316L. Stainless is typically applied where additional strength and rust/corrosion resistance are required. Biggest drawback? The cost! Let’s look at the differences between 304 and 316L:
Stainless 304
- Available in two finishes: mill, which is flat, and #4, which is shiny
- Extreme durability and strength available in gauges 24-16 based on size and needs
- Industrial / commercial applications
- Can be powder coated – but typically isn’t
Stainless 316L
- Strongest and most durable offering
- For intense weather, rust/corrosion applications. Also ideal for damage prone applications.
- Available in gauges 24-16 based on side and needs
- The most expensive choice – but unrivaled for extreme applications, such as Naval and other maritime uses
- Can be powder coated – but typically isn’t
Aluminum – the ideal choice for lightweight applications. These include doors, shutters and grilles operated manually or with a hand chain.
- Lightweight, corrosion/weather resistant
- Available in Mill finish or clear anodized
- Available in gauges 20-16 based on side and needs
- Doesn’t need to be painted, but can be powder coated
Powder Coating (Steel & Aluminum) – galvanized, stainless steel and aluminum can all be powder coated in hundreds of standard colors. In addition, color matching is also available if you need to get really precise. This option is typically used where aesthetics are a top concern. The biggest drawback is added cost.
- Most customizable. RAL color match is typically offered
- Super durable option for fade resistance is available for intense heat locations, as found in tropical climates
- High cycle options available – to help prevent scratching and maintain color integrity
- Thicker than baked enamel
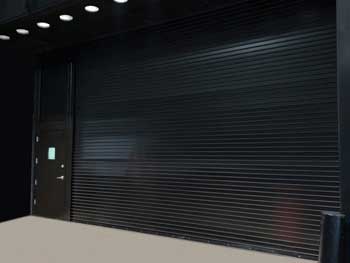
As you can see, there are plenty of options available for rolling door materials and finishes. However, it’s critical to make sure that you select the right configuration for your specific application and usage. When aesthetic considerations and environmental conditions are of concern, the extra up front investment pays off in the long run. Doors will maintain their look, integrity and last.